SWAROVSKI OPTIK has been producing premium long-range optical devices in Tyrol since 1949. Production processes at its headquarters in Absam, Tyrol – the heart of the company – are cutting-edge and continually optimized. In recent years, the issue right at the top of the agenda has been ‘digitalization of production processes,’ with the implementation of a Manufacturing Execution System (MES). The objectives were clear: how can production be made even more sustainable across the entire value chain? How can efficiency be increased, and potential improvements fully exploited? These factors are essential for sustainable economic growth, a strong location, and jobs.

AN INNOVATIVE DIGITAL
PRODUCTION NETWORK
As part of a comprehensive and innovative project, the Tyrolean family-owned company has progressively integrated production processes for its two brands, SWAROVSKI OPTIK and KAHLES, at its three sites (Absam, Austria; Guntramsdorf, Austria; Cranston, North America) into a homogeneous digital network. The aim is to digitally map all production and logistics processes in the Manufacturing Execution System and allow complete simulation. Since mid-2022, all 200 production workstations have been mapped in the system, including machines and manual workstations.

BENEFITS
AT A GLANCE
This innovative system means that each step in the production process is now visible, live data on machine running times and quantities are always visible, and comprehensive reports can be generated at the touch of a button. This brings a wide range of benefits for employees, including real-time control of production, as teams can now react immediately to live information.
Since the implementation, SWAROVSKI OPTIK has
increased production efficiency with associated savings in resources and costs – still with the same premium quality, of course
streamlined cooperation within teams – e.g. during shift handovers, etc.
kept energy consumption constant despite increasing production volumes, even achieving reductions in some cases, thanks in part to more efficient production processes
retained great flexibility for the future. New systems and machines can be integrated seamlessly
immediately recognized optimization potential, allowing appropriate improvement measures to be defined in daily meetings
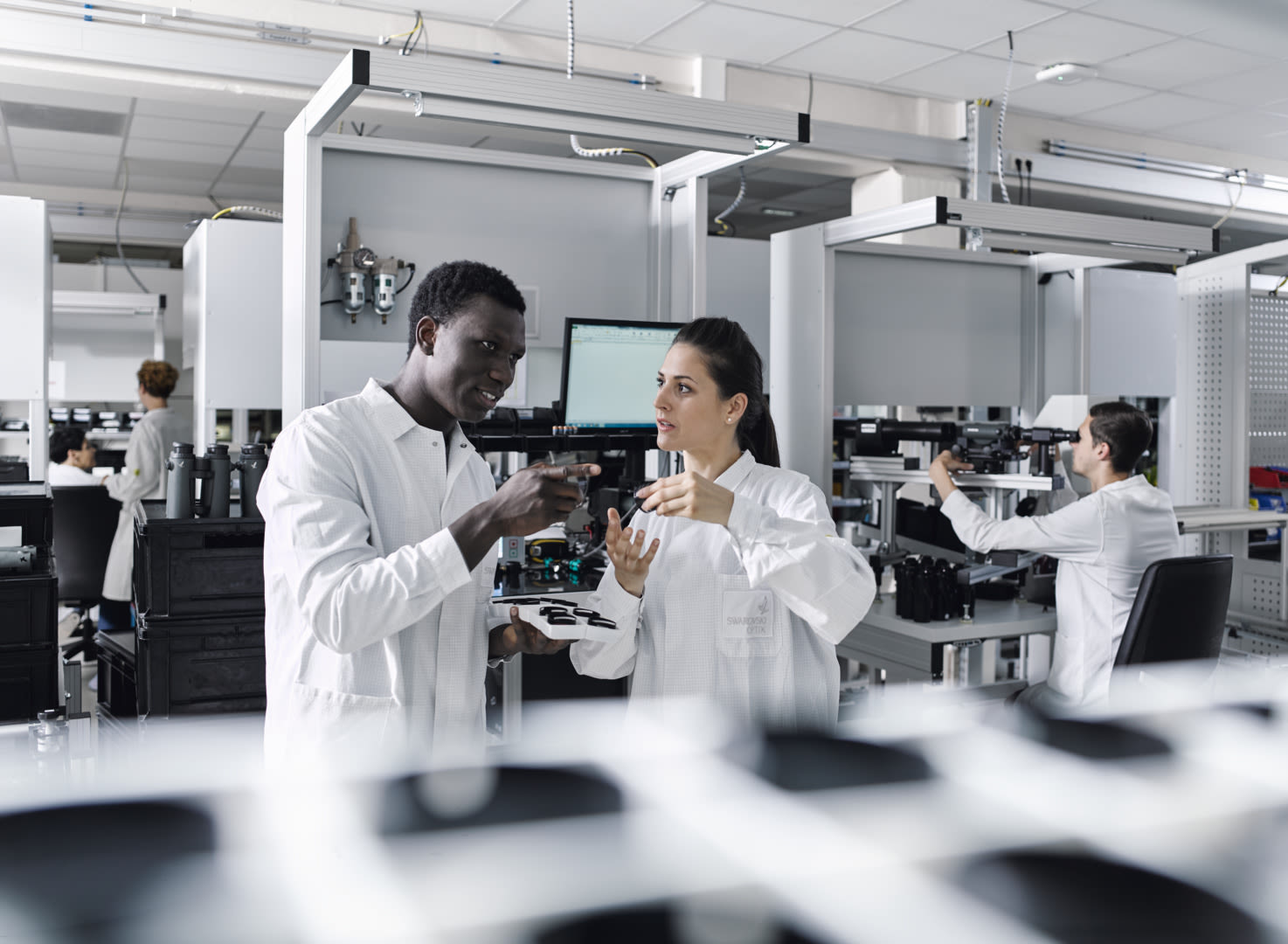
SWAROVSKI OPTIK naturally applied its traditional high quality standards to the system software. Many functions and features have been customized for our company and its requirements to ensure an optimum result. And the benefits are clear.
WHAT NEXT?
SWAROVSKI OPTIK has set new standards with this innovative system. But our production will continue to develop in the future, for example by better identifying and utilizing the potential of individual machines. Open API allows the integration of collaborative robots. These are already being used and further innovations are continuously being developed and tested in the company’s robotics laboratory.
The project was implemented with Forcam as the systems partner.