Step by step
At SWAROVSKI OPTIK, we try to keep our ecological footprint as small as possible. As a visionary company, we see sustainable management as a matter of course - and as an investment in the future.
We spare no expense or effort to reduce our ecological footprint, to reduce our environmental impact or - even better - to avoid it in the first place. We pay particular attention to the following levers:
Using renewable energy sources and reducing electricity consumption
Ensure heating and cooling supply via a closed-loop system
Promote future-oriented mobility
Use sustainable packaging and
Produce locally wherever possible, not only our sport optics themselves, but also the accessories (bags)
Our ambitious goal: By 2028, 95 percent of our total energy consumption should be free of fossil fuels.


Our first photovoltaic system went into operation back in 2013. Successive expansions over the years took the number of photovoltaic modules to around 1,200 in 2021. These are capable of generating around 330,000 kWh of electricity. The latest expansion will increase the total to approximately 2,000 photovoltaic modules.

The cycle
of warm and cold
We use the heat or cold generated during certain production steps for the general heating or cooling system. A special, highly efficient closed-loop system is used for this purpose. In Austria, we were the first company to use this technology.
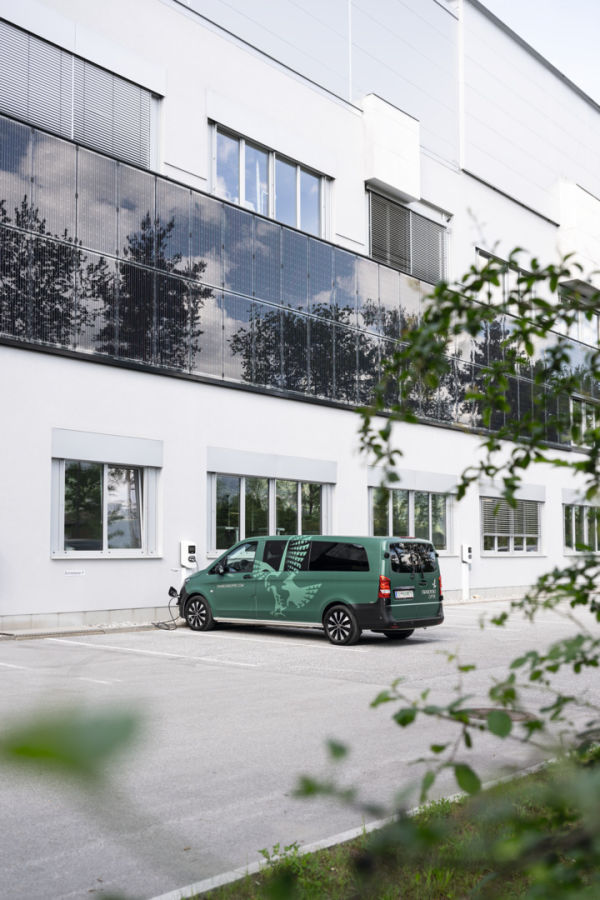
mobility
of the future
How can we reduce the number of daily car commutes made by our employees? By offering our own company buses. These bring up to 80 people to the company headquarters every day. We also offer a flexible home office arrangement. Thanks to working from home, additional miles are saved.
E-Mobility is a top priority for us. The entire company fleet is currently being converted to electric or hybrid drive. At the headquarters in Absam, up to 17 electric cars can be charged simultaneously, and four charging stations for e-bikes are also available.
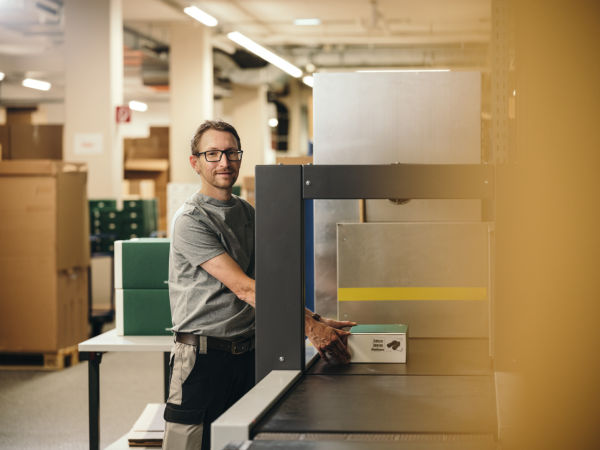
Packaging
Sustainably packaged
The packaging of our sport optics is climate-neutral - and has been since 2015. Also our accessories have also been delivered only in climate-neutral packaging since 2018. The cardboard we use is produced just three kilometers (about two miles) away from our company headquarters. The high-quality natural paper is produced especially for us at lake Tegernsee. We do not use the customary foam packaging inserts. Instead, we use custom-made cardboard inserts. Since we omit the additional protective film, recycling is possible without any problems.
Thanks to our own packaging machine, all SWAROVSKI OPTIK products can be packed extremely sturdily and securely in customized outer boxes. The result: We save filling material, valuable storage space, and CO₂ during shipping.

Local Production
of sustainable accessories
We also keep sustainability in mind when designing and manufacturing our product bags. For many, the main material as well as the lining are made of 100 percent recycled polyester (rPET), which in turn is fully recyclable. Since the company was founded in 1949, SWAROVSKI OPTIK has been committed to "Made in Tyrol, Austria." That is why, in addition to our sport optics themselves, numerous accessories are also manufactured in Austria. For example, the material for our storage bag and our cooking apron is manufactured in a small, traditional weaving mill in Austria.


To reduce electricity consumption, all lighting is gradually being converted to LEDs. Already, about 80 percent of the interiors and all parking spaces are illuminated by LEDs.
Our sustainability efforts are guided by the Sustainable Development Goals of the United Nations.

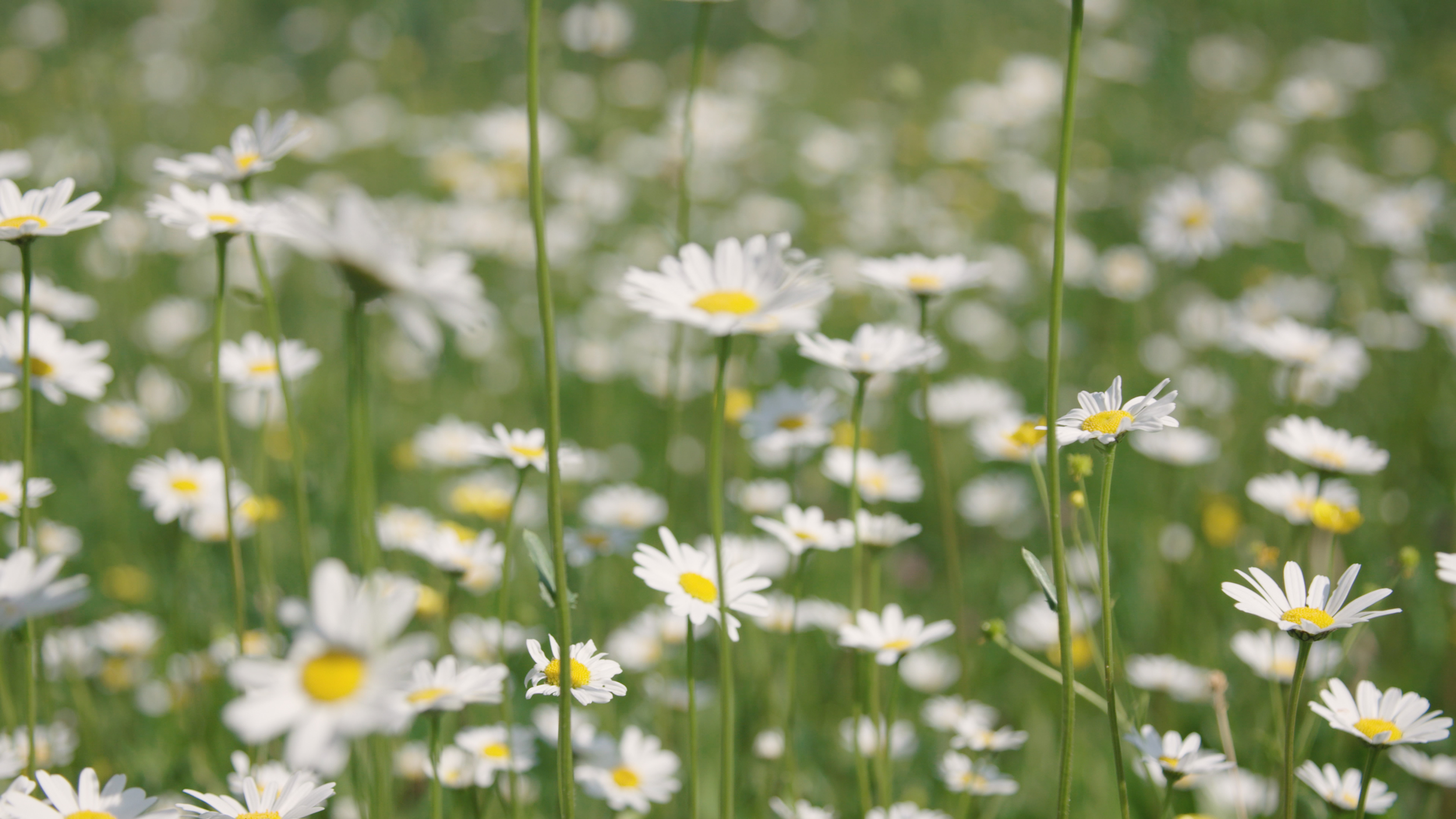